Table of Contents
ToggleStainless steel AISI 316L powder is a highly versatile material used across various industries for its excellent corrosion resistance, mechanical properties, and weldability. This article provides a comprehensive overview of 316L stainless steel powder covering its properties, production methods, applications, suppliers, costs, installation, operation, and maintenance.
Overview of stainless steel aisi 316l powder
Stainless steel 316L powder is a variation of grade 316 stainless steel that contains low carbon content to minimize carbide precipitation during welding. The ‘L’ denotes the lower carbon content compared to standard 316 steel. The composition is provided below:
Table 1: Chemical composition of stainless steel 316L powder
Element | Weight % |
---|---|
Iron (Fe) | Balance |
Chromium (Cr) | 16-18 |
Nickel (Ni) | 10-14 |
Molybdenum (Mo) | 2-3 |
Manganese (Mn) | ≤ 2 |
Silicon (Si) | ≤ 1 |
Carbon (C) | ≤ 0.03 |
Phosphorus (P) | ≤ 0.045 |
Sulfur (S) | ≤ 0.03 |
Nitrogen (N) | ≤ 0.1 |
The key highlights of 316L stainless steel are:
- Excellent corrosion resistance comparable to 316 grade steel
- Improved weldability and reduced sensitization effects
- Can be readily welded without preheating
- Withstands pitting and crevice corrosion in harsh environments
- High strength and hardness retention at elevated temperatures
- Easily fabricated into various parts using powder metallurgy
- Non-magnetic austenitic structure
316L powder provides the same advantages of bulk 316L alloy in powder form suitable for additive manufacturing or powder metallurgy parts production. The fine powder morphology allows complex net shape components to be produced without extensive machining.
Table 2: Physical properties of 316L stainless steel powder
Properties | Unit | 316L SS |
---|---|---|
Density | g/cm3 | 7.9 |
Melting point | °C | 1375-1400 |
Thermal conductivity | W/m-K | 16.3 |
Electrical resistivity | μΩ-cm | 72 |
Modulus of elasticity | GPa | 193 |
Poisson’s ratio | – | 0.30 |
Specific heat capacity | J/g-°C | 0.50 |
Production Methods for stainless steel aisi 316l powder
316L stainless steel powder can be produced using the following methods:
Table 3: Production methods for 316L stainless steel powder
Method | Description | Characteristics |
---|---|---|
Gas atomization | Molten steel stream broken into fine droplets and rapidly solidified by inert gas | Spherical powder, good flowability, high purity |
Water atomization | Molten steel stream broken into droplets by high pressure water jet | Irregular powder, high oxygen content |
Plasma atomization | Molten steel stream atomized into finer droplets by plasma torch | Very fine spherical powder, alloyed compositions |
Mechanical alloying | Elemental/prealloyed powders milled to achieve alloy composition | Irregular powder, contamination risk |
Electrolysis | Aqueous electrolytic process to deposit alloy powder | Dendritic powder, high purity |
Metal injection molding | Fine powders mixed with binders and injection molded | Control over shape and size |
Gas atomization is preferred for additive manufacturing applications due to the spherical morphology and smooth surface of powders. Mechanical alloying and electrolysis methods allow custom alloy compositions to be produced. The powder production method controls characteristics like particle shape, size distribution, flowability, purity, and microstructure.
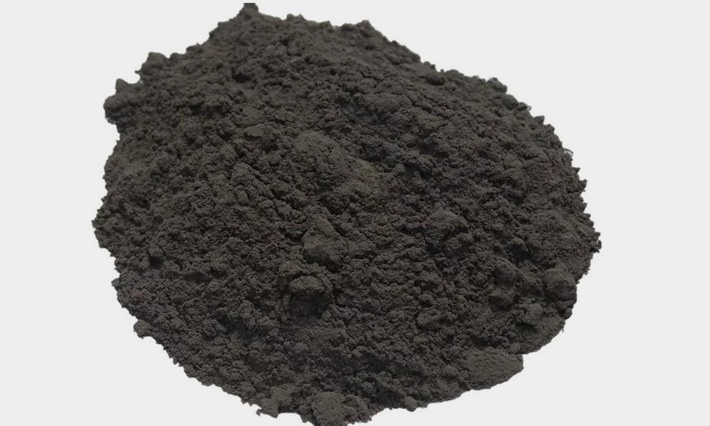
Applications of stainless steel aisi 316l powder
Some major applications of 316L stainless steel powder include:
Table 4: Applications of 316L stainless steel powder
Industry | Applications |
---|---|
Aerospace | Engine components, fittings, fasteners, brackets |
Automotive | Valves, pistons, exhaust components, clamps, springs |
Chemical | Pipes, vessels, pumps, valves, flanges, fittings |
Oil & gas | Downhole tools, drill collars, wellhead parts,christmas trees |
Medical & dental | Implants, surgical instruments, prosthetics |
Food processing | Vessels, tubing, valves, fittings, fasteners |
Marine | Propeller shafts, diesel engine parts, deck equipment |
Additive manufacturing | Aerospace, automotive, medical parts production |
The key drivers for using 316L powder are corrosion resistance, ability to withstand prolonged exposure to acids, solvents, salts, or chlorides, high temperature stability, and biocompatibility for medical implants and devices. Components made using 316L powder metallurgy also have isotropic properties unlike wrought or cast alloys.
Specifications for stainless steel aisi 316l powder
316L powder used in various applications must conform to material and process specifications as below:
Table 5: 316L stainless steel powder specifications
Parameter | Specification |
---|---|
Alloy grade | 316L per ASTM A240 |
Particle shape | Predominantly spherical |
Particle size | 15-45 microns |
Apparent density | > 90% of theoretical density |
Tap density | ≥ 4 g/cm3 |
Flow rate | ≤ 25 s/50 g |
Carbon content | ≤ 0.03 wt% |
Oxygen content | ≤ 0.1 wt% |
Nitrogen content | ≤ 0.1 wt% |
Hydrogen content | ≤ 0.015 wt% |
Surface oxide | Thin passivating layer |
Microstructure | Austenitic, equiaxed grains |
The particle size distribution depends on the intended application method like laser powder bed fusion, binder jetting, or metal injection molding. Finer particle sizes allow higher resolution but poorer flowability.
Design Considerations for stainless steel aisi 316l powder
Various design factors must be considered when designing components from 316L powder:
Table 6: 316L powder component design considerations
Parameter | Recommendations |
---|---|
Wall thickness | ≥ 1 mm for laser-based AM |
Surface finish | Dependent on AM process, may need post machining |
Tolerances | ± 0.1-0.3% with AM, higher for powder metallurgy |
Orientation | Build direction can affect properties |
Supports | Required in AM, minimize overhangs |
Hole features | ≥ 1 mm diameter, avoid blind holes |
Internal channels | ≥ 1 mm width, avoid long unsupported spans |
Embossed/engraved text | ≥ 1 mm height, avoid fine details |
Sharp corners | Round with 1 mm radius |
The component design must account for limitations of the specific additive manufacturing process to be used and facilitate post-processing like hot isostatic pressing, heat treatment, surface finishing, etc. Design optimizations like lattices, lightweighting, and consolidations should also be evaluated.
Suppliers and Costs of stainless steel aisi 316l powder
Some leading global suppliers of 316L stainless steel powder include:
Table 7: 316L stainless steel powder suppliers
Company | Location | Production Methods |
---|---|---|
Sandvik | Sweden | Gas atomization |
Carpenter Technology | USA | Gas atomization |
Praxair | USA | Gas atomization |
Höganäs | Sweden | Water atomization |
CNPC Powder | China | Gas atomization |
Table 8: 316L stainless steel powder price range
Powder grade | Particle size | Price range |
---|---|---|
316L | 15-45 microns | $50-$120/kg |
Plasma atomized 316L | 15-45 microns | $80-$250/kg |
Gas atomized 316L | 5-15 microns | $100-$500/kg |
Prices vary based on particle size distribution, production method, purity levels, supplier, and purchase volume. Plasma atomized and finer gas atomized powders command higher prices due to precise control over powder characteristics.
Installation of 316L Powder Based Components
The installation process for 316L powder based components depends on the manufacturing process:
Table 9: 316L powder component installation methods
Method | Installation Procedure |
---|---|
Additive manufacturing | Post-processing like supports removal, stress relieving, machining before installation |
Powder injection molding | Debinding, sintering, and finishing before installation |
Powder metallurgy | Compaction, sintering, finishing, inspection prior to installation |
Components may require joining to other parts or additional welding in place. The corrosion resistance, strength levels, and design conformance must be verified prior to installation. Proper joint design, sealants, fasteners, gaskets, and isolation pads should be utilized as needed. Personnel must follow applicable safety procedures for handling, lifting, and installing metallic parts.
Operation and Maintenance of 316L Parts
316L powder components should be operated as per design specifications to ensure performance reliability:
Table 10: 316L powder component operation guidelines
Parameter | Recommendations |
---|---|
Operating temperature | Up to 700°F for prolonged service |
Pressure rating | ~20,000 psi |
Loads | Within design load limits |
Thermal cycles | Avoid excessive thermal fatigue conditions |
Corrosive exposure | Avoid prolonged exposure to chlorides >150°F |
Routine maintenance is advised:
- Inspect for damage, cracks, wear
- Check for leaks, OD corrosion, deposits
- Test mechanical integrity
- Clean surfaces, remove deposits
- Lubricate moving parts
Replacement may be needed in case of powder degradation, embrittlement, fatigue, or other failure modes. Personnel must exercise caution when handling failed powder metallic components due to fracture, debris, or other hazards.
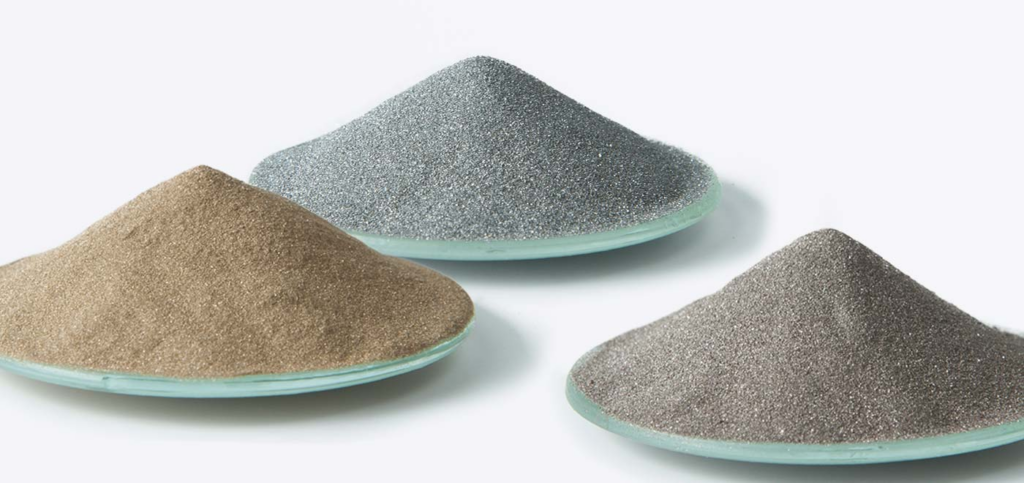
How to Select a Reliable 316L Powder Supplier
Buyers should evaluate 316L powder suppliers on the following aspects:
Table 11: Guidelines for selecting 316L powder supplier
Parameter | Recommendations |
---|---|
Powder manufacturing capabilities | Advanced gas atomization or plasma capacity |
Powder certification | ISO 9001, AS9100 quality system |
Testing capabilities | Particle size, morphology, chemical analysis |
Inventory and lead times | Stock availability for quick delivery |
Technical expertise | Metallurgy and powder production knowledge |
Customer service | Responsive sales and technical support |
Pricing | Competitive pricing for required grade and particle size |
Logistics | Capable of timely domestic/international delivery |
Reputable suppliers like Sandvik, Carpenter, Praxair with decades of powder experience should be preferred. The buyer must evaluate if the supplier can consistently provide 316L powder meeting their specifications at a reasonable cost.
Pros and Cons of 316L Stainless Steel Powder
Table 12: Advantages and limitations of 316L stainless steel powder
Advantages | Limitations |
---|---|
Excellent corrosion resistance | Expensive compared to carbon steel powder |
Outperforms 304 grade powder | Lower strength than precipitation hardening alloys |
Improved weldability over 316 powder | Subject to pitting and crevice corrosion |
High temperature oxidation resistance | Requires post-processing after AM build |
Can be readily welded and fabricated | Limited supplier and alloy availability |
Biocompatible for medical implants | Poor creep rupture strength |
Powder metallurgy allows complex shapes | Difficult to cut and machine in hardened state |
Near net shape parts from AM | Lower fatigue strength than wrought product |
For critical applications, buyers must evaluate if the superior corrosion resistance, weldability, and biocompatibility justify the higher cost over other stainless, tool steel, cobalt, or nickel-based powders grades. Component testing is recommended to verify 316L powder parts meet design requirements.
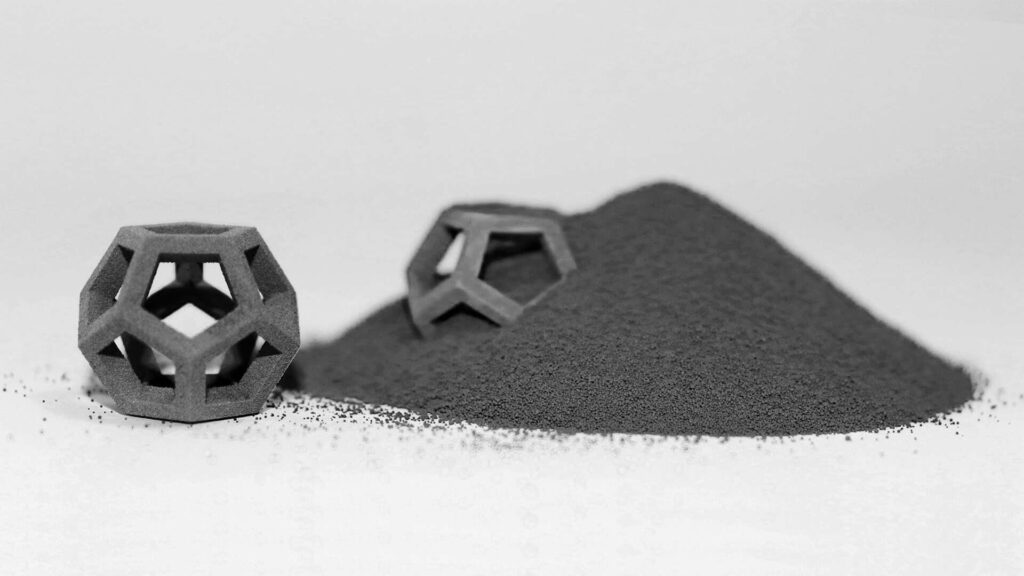
Stainless Steel 316L Powder – Frequently Asked Questions (FAQ)
Q: What is the difference between 316 and 316L stainless steel powder?
A: 316L powder has lower carbon content (0.03% max) than 316 powder (0.08% max) to provide better weldability and corrosion resistance.
Q: What are the alternatives to 316L powder?
A: Alternatives include 304L, 317L for weldability; 904L, 254SMO, AL-6XN for corrosion resistance; and 17-4PH, 15-5PH for high strength.
Q: What powder size is best for laser melting 316L powder?
A: 15-45 micron powder is recommended for most laser powder bed fusion applications to balance flowability and resolution.
Q: What are the typical impurities in 316L stainless steel powder?
A: Impurities can include oxygen, nitrogen, hydrogen, sulfur, carbon, silicon, manganese, chromium, nickel, molybdenum, copper, cobalt.
Q: What post processing is required for additively manufactured 316L parts?
A: Post processing includes supports removal, stress relieving, HIP, machining, grinding, polishing, passivation, and testing.
Q: What are common applications for 316L powder?
A: Marine hardware, chemical processing equipment, oil & gas tools, medical implants, aerospace engine parts, food processing equipment.
Q: Does 316L powder require hot isostatic pressing?
A: HIP helps improve densification, reduce porosity, and enhance mechanical properties of AM 316L parts but is not always mandatory.
Q: Is 316L stainless steel powder susceptible to corrosion?
A: 316L has excellent corrosion resistance but is still susceptible to pitting and crevice corrosion from prolonged chloride exposure above 60°C.
Q: What is the typical surface finish of as-built 316L AM parts?
A: Surface roughness (Ra) values of 10-25 microns are common for AM 316L parts. Post-processing can improve this <1 micron if needed.