Table of Contents
ToggleOverview of 3d print tungsten
Tungsten, also known as wolfram, is a hard, dense metal with excellent high temperature strength, making it ideal for applications requiring high stiffness, wear resistance, or high temperature performance up to 1000°C. Tungsten has a density of 19.3 g/cm3, making it twice as dense as steel and close to pure uranium in density.
3D printing of tungsten and tungsten alloys allows parts to be produced in complex geometries not possible with traditional manufacturing methods. The high stiffness and wear resistance of tungsten makes it suitable for 3D printing mold tooling, electrodes, radiation shielding components, ballast weights, and other applications requiring high density material properties.
Tungsten can be 3D printed using powder bed fusion technologies including selective laser melting (SLM) and electron beam melting (EBM). Both methods work by selectively melting layers of tungsten powder to build up a solid 3D part. The major considerations for 3d print tungsten include part design, powder selection, print process parameters, post-processing, and material properties.
This article provides a complete guide to 3D printing with tungsten covering:
- Key applications of 3D printed tungsten parts
- Types of tungsten metal powders
- Selective laser melting and electron beam melting process overview
- Print parameters and considerations
- Post-processing procedures
- Mechanical properties and microstructure
- Suppliers and cost analysis
- Design principles and limitations
- Comparison to alternative manufacturing processes
- Advantages and disadvantages of the technology
Key Applications of 3D Printed Tungsten Parts
Tungsten is applied in 3D printing for products requiring high density, stiffness, hardness, and temperature resistance. Typical applications include:
طلب | Description |
---|---|
Radiation shielding | Tungsten’s density blocks harmful gamma and x-rays. Used in medical, nuclear, and aerospace fields. |
Vibration damping | Tungsten’s density damps vibrations effectively. Used for precision instruments. |
Ballast weights | High density balances and calibrates systems precisely. |
Electrode contacts | Withstands arcing. Used in electrical contacts and vacuum interrupters. |
Automotive | Tungsten alloys in high performance auto components. |
Mining | Wear-resistant tungsten carbide mining and drilling tools. |
Aerospace | Rocket nozzles, turbine blades, and other high-temp components. |
Military | Kinetic energy penetrators, armor-piercing ammunition. |
Medical | High stiffness scalpels, dental tools, bone screws. |
3D printing enables complex tungsten part geometries not feasible with subtractive machining, expanding applications across industries needing high performance metal properties.
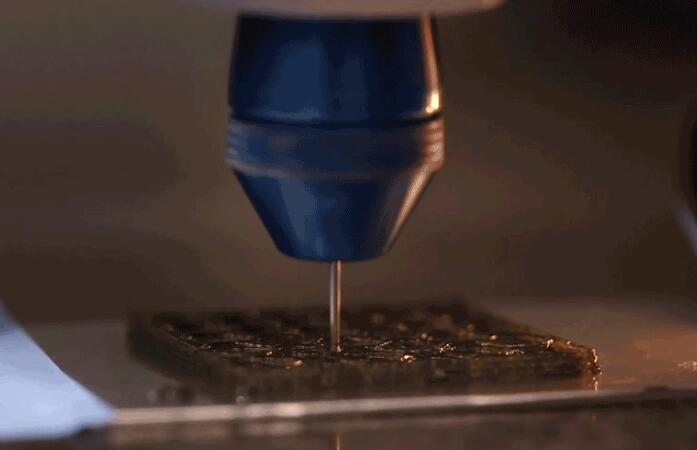
Types of Tungsten Metal Powders for 3D Printing
Tungsten is available in different powder types for use in powder bed fusion 3D printing processes:
Powder Type | Description | Particle Shape | Particle Size |
---|---|---|---|
Pure tungsten | Elemental tungsten, 99.9% purity | Spherical | 15-45 microns |
Tungsten carbide | Tungsten carbide-cobalt cermet | Spherical/irregular | 45-150 microns |
Tungsten alloys | Tungsten heavy alloys with nickel, iron or copper | Spherical | 15-45 microns |
Pure tungsten is preferred for laser powder bed fusion due to its higher melt temperature compared to tungsten alloys. Tungsten carbide grades contain a cobalt binder and are harder but more difficult to process. For EBM, coarser powders up to 150 microns can be used.
Spherical powders deliver better flow and packing density. Smaller particle sizes below 45 microns improve resolution, surface finish, and sintering. However, handling very fine powders requires caution for powder flammability.
Overview of Selective Laser Melting Process for Tungsten
Selective laser melting (SLM) uses a laser beam to selectively fuse regions of a tungsten powder bed to build up 3D objects layer by layer. The process takes place inside an inert gas chamber with oxygen levels below 0.1% to prevent oxidation.
SLM Process Steps:
- Tungsten powder is spread in thin layers across a build plate using a recoater arm.
- The laser beam traces each layer, heating powder to above melting point to create fused solid regions.
- The build plate drops down slightly and new powder layer is spread over the previous layer.
- Steps repeat until full part is built up from tungsten metal powder.
- Unfused powder supports overhangs and undercuts during printing and is recycled after.
- High temperatures up to 3000°C are generated from laser melting localized powder spots.
- Parts are then removed from powder cake and post-processed.
SLM allows printing complex geometries directly from a 3D CAD model not possible with casting or machining. Fine 0.02-0.05 mm resolution and smooth surfaces are achieved.
Key SLM Print Process Parameters for Tungsten
Optimizing SLM print parameters is critical to achieve high density tungsten parts with controlled microstructure and mechanical properties.
Print Parameter | Typical Range | Role |
---|---|---|
Laser power (W) | 100-400 W | Melts powder efficiently. Higher power increases build rate. |
Scan speed (mm/s) | 100-1000 mm/s | Speed of laser traversing each layer. Affects energy input. |
Hatch spacing (μm) | 50-200 μm | Distance between scan lines. Affects overlap and densification. |
Layer thickness (μm) | 20-100 μm | Thin layers improve resolution but slow down builds. |
Focus offset (mm) | 0 to -2 mm | Defocuses spot for wider melt pool and better layer bonding. |
Preheating temperature (°C) | 100-400 °C | Heats powder bed to reduce thermal stresses. Improves layer bonding. |
These parameters must be balanced to provide sufficient energy for melting while minimizing residual stresses from steep thermal gradients.
Post-Processing Methods for SLM Tungsten Parts
After the SLM build process, additional post-processing is needed to obtain a finished tungsten part:
- Removal from powder bed – Parts are dug out from surrounding unconsolidated powder carefully.
- Support removal – Supports are cut off the part manually or chemically dissolved.
- Thermal stress relief – Annealing at 1000-1500°C relieves residual stresses and improves ductility.
- Hot isostatic pressing – HIPing at over 2000°C further densifies the microstructure.
- Machining – CNC milling achieves tighter tolerances and surface finishes.
- Surface treatments – Metal coating or polishing can enhance surface properties.
Proper post-processing is key to achieve the required dimensional accuracy, microstructure, and material properties after the as-printed state.
Mechanical Properties of SLM Tungsten
Selective laser melting produces near fully dense tungsten parts with properties approaching wrought equivalents:
Property | SLM Tungsten | Wrought Tungsten |
---|---|---|
Density | Over 99% theoretical | 99.9% |
Tensile strength | 450 to 650 MPa | 550 MPa |
Yield strength | 400 to 500 MPa | 500 MPa |
Elongation | 3 to 8% | 10% |
Hardness | 300 to 400 HV | 340 HV |
Thermal conductivity | 140 to 180 W/mK | 174 W/mK |
The ultrafine microstructure from rapid solidification results in very high hardness and strength. However, crack-sensitive tungsten needs hot isostatic pressing and annealing to improve ductility.
Microstructure of SLM Tungsten
The microstructure of as-built SLM tungsten consists of fine columnar β-tungsten grains along the build direction measuring 5 to 10 microns wide and elongated several hundred microns long.
Within the columns, cellular subgrain structures up to 500 nm wide are observed, resulting from complex thermal cycling during laser scanning. The microstructure contains high dislocation density with nano-scale pores and unmelted particles between grain boundaries.
Post-process annealing recrystallizes this columnar structure into more uniform and coarser tungsten grains over 50 microns wide with reduced internal stresses and dislocation density.
Selective Laser Melting vs. Electron Beam Melting
Electron beam melting (EBM) is an alternative powder bed fusion process that uses an electron beam heat source instead of a laser.
Comparison | SLM | EBM |
---|---|---|
Heat source | Laser | Electron beam |
Atmosphere | Argon | Vacuum |
Beam control | Galvo scanner | Electromagnetic coils |
Max build size | 250 x 250 x 300 mm | 200 x 200 x 350 mm |
Resolution | 50 μm | 70 μm |
Accuracy | +/- 100 μm | +/- 150 μm |
Surface finish | Rough as-built, smooth after machining | Rough texture |
The fast beam scanning of SLM enables finer resolution and surface finish. EBM’s advantage is higher build speed and simpler powder handling in a vacuum.
Suppliers of Tungsten Powder for 3D Printing
Various manufacturers supply tungsten powders for powder bed fusion 3D printing:
Supplier | Powder Types | Particle Size | Pricing |
---|---|---|---|
Buffalo Tungsten | Pure tungsten, tungsten carbide | 10-44 μm | $100-$200/kg |
Midwest Tungsten | Pure tungsten | 10-40 μm | $80-$250/kg |
H.C. Starck | Pure tungsten, tungsten alloys | 15-45 μm | $150-$350/kg |
Nanjing Tungsten | Pure tungsten | 15-45 μm | $100-$250/kg |
Tyranna Resources | Pure tungsten | Under 45 μm | $250-$400/kg |
Powder cost ranges from $80/kg for lower purity to over $400/kg for high precision grades. Significant material is wasted as unfused powder during builds.
Cost Analysis of 3D Printed Tungsten Parts
Here is a breakdown of costs for SLM production of tungsten parts:
Cost Component | Typical Estimate |
---|---|
Tungsten powder | $100-$250 per kg |
Other raw materials | $2-$10 per build |
Machine charges | $50-$150 per hour |
Labor | $40-$100 per hour |
Post-processing | $20-$50 per part |
Total part cost | $100 per 100g up to $5000 for complex large parts |
For small parts under 100 g, expect costs of $100 per part. Larger more complex parts can cost up to $5000 due to long build times and significant raw material consumption.
Compared to machining, 3D printing in tungsten has higher part costs but enables previously impossible part geometries.
Design Principles for SLM Tungsten Parts
Optimal part design is critical to leverage 3D printing’s capabilities and avoid defects when working with tungsten:
- Use thicker walls and structures over 2 mm to prevent cracking from residual stresses.
- Minimize overhanging geometries requiring support structures.
- Include relief holes, rounds or fillets to avoid stress concentrations.
- Design enclosed volumes as lattice structures to improve powder removal.
- Orient parts to minimize unsupported overhangs and avoid long thin sections prone to deformation.
- Account for ~100 μm printing tolerance and scale parts accordingly.
- Design mating surfaces for post-machining to achieve precision fit.
- Take advantage of design freedom – consolidate assemblies into single complex parts.
Perform thermal and structural simulations to identify areas of high residual stress during design. Avoid delicate features prone to damage during post-processing.
Limitations When 3D Printing With Tungsten
Despite its advantages, tungsten also poses challenges for powder bed fusion processes:
- High density tungsten reflects laser energy, limiting absorption and build rates.
- Low thermal conductivity leads to heat buildup distorting parts.
- High temperatures and reactivity with oxygen/nitrogen during processing.
- Parts suffer brittle as-printed microstructures prone to cracking.
- Significant post-processing is required to achieve properties close to wrought.
- Maximum part size is restricted by printer build volume.
- Vertical surfaces have poor finish and require machining.
- Comparatively expensive powder material drives up costs.
Careful process control is needed to successfully print high quality tungsten components.
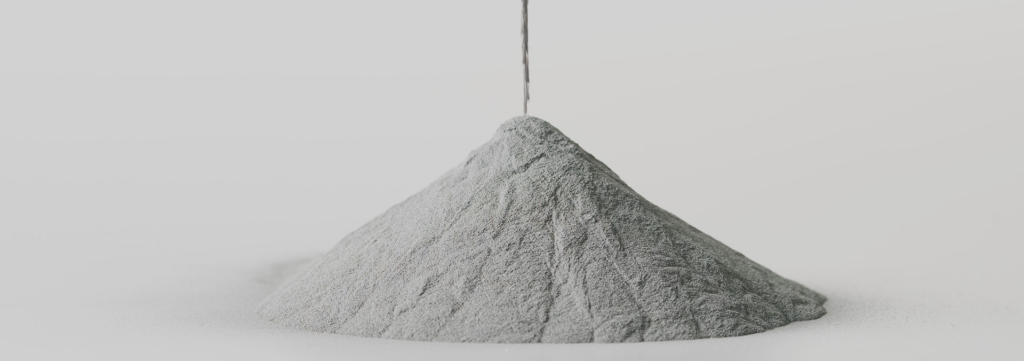
Advantages of 3d print tungsten Parts
Key benefits of additive manufacturing with tungsten include:
- Complex geometries – Produce intricate designs not possible with casting or machining tungsten.
- Consolidated assemblies – Integrate multiple components into a single printed part.
- Mass customization – Easily modify and optimize designs for each application.
- Weight reduction – Create lightweight lattices and inner structures not feasible with subtractive methods.
- High hardness – As-printed parts achieve up to 400 HV hardness.
- Quick turnaround – Shorten development time vs. traditional tooling methods.
- Part consolidation – Combine assemblies into single complex components.
- Zero waste – Unfused powder is reused rather than scrapped.
3D printing unlocks innovative new applications for tungsten across industries demanding high performance metal properties.
Disadvantages & Limitations of 3d print tungsten
- High cost – Tungsten powder is expensive. Significant unused powder is wasted in builds.
- Lower ductility – As-printed tungsten is prone to cracking without post-processing.
- Limited size – Printer build volumes restrict maximum part dimensions.
- Rough surfaces – Vertical faces have poor finish and need machining.
- Long process – Printing and post-processing time is slow for production volumes.
- Parameter sensitivity – Achieving defect-free builds requires extensive fine tuning.
- Safety issues – Tungsten powder handling requires protective equipment against flammability.
3d print tungsten is best suited for low volume production of complex, high value parts where performance outweighs cost.
The Future of 3d print tungsten
Additive manufacturing with tungsten will see further growth in:
- Expanding range of available tungsten alloys and composites.
- Larger machine build sizes enabling bigger printed parts.
- Improved powder reuse and recycling lowering material costs.
- Hybrid manufacturing combining printing and machining.
- Better understanding of process-microstructure-property relationships.
- New applications across aerospace, defense, automotive, and medical sectors.
- Directed energy deposition (DED) processes for printing large near-net shape parts.
- Standardization of printing parameters, qualifications, and certifications.
With increased adoption, 3D printed tungsten components will move from prototyping to wider production use cases.
Conclusion
3D printing offers an innovative method to manufacture high performance tungsten components with complex geometries not feasible using conventional techniques. Applications range from radiation shielding and ballast weights to electrodes and aerospace components.
The selective laser melting process can produce near fully dense tungsten parts from powder layers, but careful optimization of print parameters and post-processing is crucial to properties and performance. Although cost is still a limitation, 3D printed tungsten unlocks novel designs and customization possibilities across industries.
As processes continue improving and new tungsten alloys are developed, additive manufacturing will find increasing uses for parts demanding ultra-high density, stiffness, hardness, and heat resistance properties.
FAQ
Here are answers to some common questions about 3D printing with tungsten:
What are the main benefits of 3d print tungsten parts?
3D printing key advantages are design freedom, mass customization, consolidated assemblies, lightweight lattices, rapid prototyping, and enabling complex geometries not possible with machining or casting.
What metal 3D printing methods can process tungsten?
The selective laser melting (SLM) and electron beam melting (EBM) powder bed fusion processes are currently used for printing tungsten.
What industries use 3D printed tungsten parts?
Aerospace, defense, automotive, medical, electronics, and nuclear industries apply 3D printed tungsten components.
What types of tungsten powder can be used for 3D printing?
Pure tungsten, tungsten carbide-cobalt, and tungsten heavy alloys powders in the 10-45 micron size range. Spherical powders give best results.
Does printed tungsten require any post-processing?
Post-processes like stress relieving, hot isostatic pressing, and machining are needed to improve ductility, densification, tolerances, and surface finish.
How do the properties of printed tungsten compare to conventional tungsten?
Carefully processed printed tungsten can achieve 99% density and nearly match wrought material strength and hardness. Ductility is slightly lower.
What are some examples of end-use 3D printed tungsten parts?
Nozzle inserts, electrodes, radiation shields, counterweights, high-density ballast, balancing components, and metal cutting tools using tungsten heavy alloys.
What size tungsten parts can be 3D printed?
Current powder bed systems allow maximum components up to around 250 x 250 x 300 mm, but larger systems are in development.
Is 3D printed tungsten affordable for production use?
For moderate size parts, printing in tungsten costs $100-5000. Larger volume production is still limited by high powder costs.